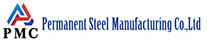
Drill pipes are crucial in oil and gas drilling operations, and rust can significantly reduce their lifespan and effectiveness.
Implementing anti-rust measures is essential for maintaining the integrity and performance of these pipes. Here are some key strategies:
1. Protective Coatings
Zinc Coating (Galvanization): Zinc acts as a sacrificial layer, corroding in place of the steel underneath.
Epoxy Coatings: These are highly resistant to chemicals and water, providing a durable barrier against rust.
Phosphate Coatings: These can enhance corrosion resistance and provide a good base for additional coatings.
Polymer Coatings: These coatings offer high resistance to abrasion and corrosion, suitable for harsh environments.
2. Use of Corrosion Inhibitors
Oil-based Inhibitors: Applied as a coating or added to drilling fluids, they form a protective layer over the pipe.
Water-based Inhibitors: Added to the drilling fluid, these chemicals inhibit rust by neutralizing the corrosive elements.
Volatile Corrosion Inhibitors (VCIs): These can be added to packaging during storage to protect pipes from rust.
3. Cathodic Protection
Sacrificial Anodes: Attach sacrificial metals like zinc or magnesium to the drill pipe to corrode instead of the pipe itself.
Impressed Current Systems: Use an external power source to drive the corrosion reaction away from the drill pipe.
4. Proper Storage and Handling
Dry Storage: Store pipes in dry, well-ventilated areas to minimize exposure to moisture.
Covering: Use protective coverings to shield pipes from rain, humidity, and other environmental factors.
Desiccants: Include moisture-absorbing materials in storage containers to reduce humidity levels.
5. Regular Maintenance and Inspection
Cleaning: Regularly clean pipes to remove mud, salts, and other corrosive substances.
Inspection: Conduct periodic inspections for signs of rust or damage and take corrective actions as needed.
6. Use of Anti-Corrosive Alloys
High-Grade Stainless Steel: More resistant to rust due to its chromium content.
Corrosion-Resistant Alloys (CRAs): Specialized alloys designed for high corrosion resistance in specific environments.
7. Internal Coatings and Linings
Plastic Liners: These provide a barrier between the pipe's internal surface and corrosive drilling fluids.
Epoxy Lining: Offers a durable internal coating that can withstand harsh chemicals and high temperatures.
8. Environmental Control
Dehumidification: Control the humidity in storage and operational environments to reduce the risk of rust formation.
Corrosion Monitoring Systems: Implement monitoring systems that detect corrosion early, allowing for timely interventions.
9. Using Corrosion-Resistant Fluids
Use drilling fluids that are less corrosive or treat the fluids with anti-corrosive additives to minimize their impact on the pipes.
10. Proper Drainage
Ensure that water and other corrosive fluids are drained from the pipes before storage to prevent internal rusting.
By combining these strategies, you can significantly extend the life of drill pipes and improve the efficiency of drilling operations.
Connecting drill pipes in correct way that minimizes rust involves several steps to ensure that the joints are protected from corrosion.
Regular monitoring and proactive maintenance are key to preventing rust and ensuring long-term performance.
Read more: Classification of Drill Pipes