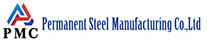
What is a burr?
Burrs are ubiquitous in the metalworking process. No matter how advanced and sophisticated equipment you use, it will be born with the product. This is mainly due to the plastic deformation of the material and the generation of excessive iron filings at the edges of the processed material, especially for materials with good ductility or toughness, which are particularly prone to burrs.
The types of burrs mainly include flash burrs, sharp corner burrs, spatters, etc., which are protruding excess metal residues that do not meet product design requirements. For this problem, there is currently no effective way to eliminate it in the production process, so in order to ensure the design requirements of the product, engineers have to work hard to eliminate it later. So far, there have been many different deburring methods and equipment for different steel pipe products.
Burr Removal of ERW Welded Pipes:
ERW (Electric Resistance Welded) pipes can sometimes have burrs or sharp edges as a result of the welding process. Removing these burrs is essential for safety, aesthetics, and to ensure the pipes meet specific industry standards. ERW welded pipe manufacturers have compiled the 9 most commonly used deburring methods for you:
1. Manual Grinding
Burr removal can be done manually using tools such as angle grinders, files, or abrasive pads. This method is effective for small-scale operations or for addressing specific areas with burrs.
2. Mechanical Deburring
Mechanical deburring machines can be used to automate the process of removing burrs. These machines often employ brushes, rollers, or other abrasive tools to smooth the edges of the pipes.
3. Abrasive Belt Deburring
Abrasive belts, either handheld or mounted on machinery, can be used to grind away burrs. This method provides a more controlled and consistent deburring process.
4. Rotary Deburring
Rotary deburring tools are designed to remove burrs from the internal and external surfaces of pipes. These tools are often adjustable to accommodate different pipe sizes and can be used in a production line setting.
5. Chemical Deburring
Chemical deburring involves using specific chemical solutions that dissolve or break down the burrs without affecting the underlying metal. This method is more suitable for specific applications and materials.
6. Water Jet Deburring
High-pressure water jets can be used to remove burrs from the pipes. This method is effective for softer materials and can be automated for large-scale production.
7. Tumbling or Vibratory Finishing
Tumbling or vibratory finishing machines use abrasive media and can be effective for deburring large quantities of small pipes. The pipes are placed in a drum or chamber, and the movement of the media removes burrs.
8. Plasma Cutting
In some cases, plasma cutting is used as a precision method to cut and remove burrs simultaneously. This is particularly useful for pipes that require accurate and clean edges.
9. Laser Deburring
Laser technology can be used for precise deburring, especially for intricate shapes and small parts. It is a non-contact method that can be automated for efficiency.
Whichever method is chosen, it is important to consider the specific requirements of the application, the type of materials used, and the surface treatment required. Additionally, safety measures should be taken and any method chosen should comply with industry standards and regulations. Regular inspections after the deburring process ensure the quality and safety of ERW welded pipes.
Tips: ASTM A53 Grade B ERW is more popular than other grades. These pipes can be bare pipes without any coating, or it may be Hot-Dipped or Zinc-Coated and manufactured by Welding or by a Seamless manufacturing process. In Oil and Gas, A53 grade pipes are used in the structural and non-critical applications. In the application of submarine oil and gas pipeline engineering, oil drills and petrochemical companies use welded pipes for gasoline, kerosene, diesel and other pipelines. ERW welded pipes are safe and economical.