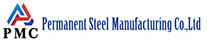
410 Stainless Steel
Type 410 Stainless Steel sheet and strip is covered by the following specifications:AMS 5504, ASTM A240.
Chemical Composition:
Element | Type 410 |
Carbon | 0.08 – 0.15 |
Manganese | 1.00 max. |
Sulfur | 0.030 max. |
Phosphorus | 0.040 max. |
Silicon | 1.00 max. |
Chromium | 11.5 – 13.5 |
Nickel | 0.75 max. |
Mechanical Properties:
Type | Yield Strength 0.2% offset (KSI) | Tensile Strength (KSI) | % Elongation (2" Gauge length) | Hardness Rockwell |
410 Ann | 30 min. | 65 min. | 20 min. | HRB 96 |
Formability
Type 410 has reasonably good cold working properties and can be moderately drawn and formed in the annealed condition.
Heat Treatment
Annealing: Heat slowly to 1500 – 1650 °F (816 – 899 °C), cool to 1100 °F (593 °C) in furnace, air cool.
Process Annealing: Heat to 1350 – 1450 °F (732 – 788 °C), air cool.
Hardening: Heat to 1700 – 1850 °F (927 – 1010 °C), air cool or oil quench.
Follow by stress-relief or temper.
Stress Relieving: Heat at 300 – 800 °F (149 – 427 °C) for 1 to 2 hours, air cool.
Tempering: Heat to 1100 – 1400 °F (593 – 760 °C) for 1 to 4 hours, air cool.
Weldability
The martensitic class of stainless steels has limited weldability due to its hardenability. Preheating to 550 °F (260 °C) is generally not required for thin sheet sections of this lower chromium martensitic stainless steel. Post-weld heat treatment should be considered to achieve required properties. This particular alloy is generally considered to have the best weldability of this stainless class. A major difference is the lower carbon content for this alloy which eliminates the need for post-weld heat treating. When a weld filler is needed, AWS E/ER 410, 410 NiMo, and 309L are most often specified. Type 410 is well known in reference literature and more information can be obtained in this way.