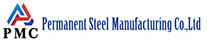
The oil drill pipe, also known as the drill string, is a key component connecting the drill bit and the drilling rig. It is responsible for transmitting the rotational power of the drilling rig to the drill bit, enabling the drill bit to drill into the formation and achieve the purpose of oil exploration and exploitation. Drill pipes are usually made of high-strength, high-toughness alloy steel to ensure that they can withstand huge pressure and torque in complex underground environments.
During oil exploration, the drill pipe not only needs to have sufficient strength and rigidity to cope with the complexity of the formation and the depth of drilling, but also needs to have good wear resistance and corrosion resistance to ensure drilling efficiency and the service life of the drill pipe. In addition, with the continuous development of oil exploration technology, the performance requirements for drill pipes are getting higher and higher, such as requiring drill pipes to have higher fatigue strength, better sealing performance, and more convenient maintenance methods, etc. Therefore, oil drill pipes are an indispensable and important tool in oil exploration.
How are the characteristics of oil drill pipes different from traditional steel?
1. Oil drill pipes are very different from traditional steel in many aspects. Oil drill pipes are usually made of alloy steel, and their alloy composition can be adjusted according to specific needs to improve properties such as wear resistance, corrosion resistance, strength and hardness. Traditional steel materials are mostly carbon steel or stainless steel, which have average performance and cannot meet the extreme environmental requirements during oil exploration and production.
2. Oil drill pipe has higher corrosion resistance, strength and hardness, and can maintain stable performance in the high temperature, high pressure and strong corrosion environment of the oil field, prolong service life and reduce maintenance costs. Traditional steel is mainly used in construction, manufacturing and other general fields, and its performance requirements are relatively low, which cannot meet the special needs of the oil industry.
3. The manufacturing process of oil drill pipe is more rigorous and complex, including precise heat treatment, forming and surface treatment processes to ensure product quality. In particular, special welding and heating treatment processes are used at the connection between the joint and the pipe body to enhance the strength and sealing of the connection. In comparison, the manufacturing process of traditional steel is relatively simple, mainly cold and hot rolling and cutting and forming, without the need for overly complicated processing processes.
4. The specifications and sizes of oil drill pipes are large, usually 4-6 inches in diameter, up to thousands of feet in length, and heavy. This large-size oil drill pipe is suitable for deep and ultra-deep well drilling operations and needs to withstand large torsion, tension, and impact loads. Traditional steel specifications and sizes are relatively small and are more common in the construction and manufacturing fields. Its size and weight depend on the specific application scenario.
5. Oil drill pipes are mainly used for drilling operations in the process of oil exploration and production, and are an indispensable and important equipment in the oil industry. Traditional steel has a wider range of applications and can be used in many fields such as construction, manufacturing, transportation, and energy.
6. The manufacturing and use costs of oil drill pipes are relatively high due to the use of high-performance alloy steel and complex manufacturing processes. Special equipment and technology are required for production and maintenance. Traditional steel, on the other hand, has a relatively low cost due to its wide range of applications and relatively simple manufacturing processes.
Read more: Production Process of Oil Drill Pipes