What are pipe fittings and pipes? How are they connected?
Pipes and pipe fittings are the basic building blocks of piping systems, each with different functions and characteristics.
Pipe refers to the material used to make the body of a pipe that has a hollow section and a length that is much greater than its diameter or circumference. There are many types of pipes, including but not limited to steel pipes, PPR pipes, PVC pipes, copper pipes, fiber pipes, composite pipes, galvanized pipes, etc. These pipes are widely used in construction projects, power plants, chemical plants and other fields to transport fluids and powdery solids, exchange heat energy, and manufacture mechanical parts and containers.
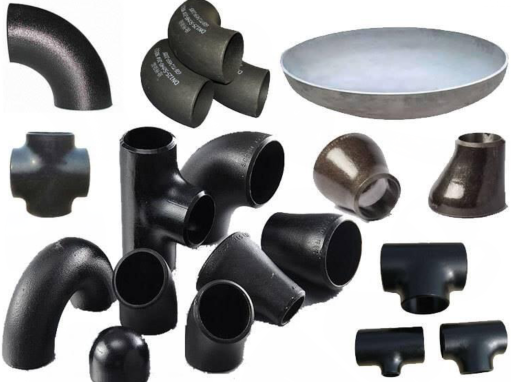
Steel pipe is one of the common pipes. It is divided into round, square, rectangular and special-shaped according to the cross-sectional shape. It is divided into carbon structural steel, low alloy structural steel, alloy steel and composite steel pipe according to the material. It is divided into transportation pipeline according to the purpose. For use in steel pipes, engineering structures, thermal equipment, etc., they are divided into seamless pipes and welded pipes according to the production process.
Pipe fittings are components used to connect pipelines. They play a role in connecting, controlling, changing direction, diverting, sealing, supporting, etc. in the pipeline system. Pipe fittings include but are not limited to water seals, tees, branch pipe seats (stands), etc. The quality of these pipe fittings directly affects the service life of the pipe, so it is very important to choose appropriate pipe fittings in hydropower renovation projects. Common pipe fittings include: flanges, bolts and nuts, washers, gaskets, elbows, tees and reducers, etc.
Common ways of connecting pipe fittings to pipes include the following:
1. Threaded connection
This is a common connection method in which internal and external threads on pipes and fittings are screwed together to create a tight connection. It is simple and easy to operate and suitable for low pressure and small diameter piping systems.
2. Flange connection
Pipes and fittings are held together by flanges and flange gaskets. Flange connections can be divided into flat welding flanges and butt welding flanges, which are usually used in large and high-pressure pipeline systems.
3. Welding connection
Pipes and fittings are welded together to create a permanent connection. Common welding connection methods include butt welding, fillet welding and socket welding. Welded connections are commonly used in piping systems with high pressures and temperatures.
4. Clamp connection
Use clamps to clamp pipes and fittings together to create a connection. This type of connection is suitable for smaller diameter pipe systems such as water pipes and irrigation systems.
5. Grooved connection
Using hooks or groove connections, special tools are used to machine grooves on the pipe, and then clamps are used to clamp the pipe and fittings together.
6. Pressure connection
This is a common connection method that uses special pressure tools to compress sleeves or sleeves on pipes and fittings to form a sealed connection. Common pressure connection methods include ferrule connection, pressure sleeve connection and link connection. Pressure connections are suitable for piping systems made of many different materials.
7. Tension connection
Connections are made by clamping pipes and fittings together using bolts and nuts. This connection method is suitable for large pipelines and high-pressure pipeline systems.
8. Quick connection
Quickly connect pipes and fittings to create a connection using quick connectors or quick connectors. This connection method is suitable for occasions that require frequent disassembly and replacement, such as liquid transmission and gas transmission.
Conclusion:
The above are common ways of connecting pipe fittings to pipes. Choosing the appropriate connection method should be determined based on the specific pipeline system requirements and application scenarios. Before proceeding with installation, be sure to refer to relevant design and specification requirements and follow the installation guidelines provided by the manufacturer