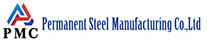
304 stainless steel pipes are made from a versatile austenitic stainless steel alloy that contains chromium (18%) and nickel (8%). This composition provides excellent corrosion resistance, high strength, and good fabrication characteristics.
Types of 304 SS Pipes:
Seamless: Manufactured without a seam and typically used for high-pressure applications.
Welded: Created by welding two edges together, suitable for lower pressure applications.
The welding connection method of 304 stainless steel pipe is to use the hot melt processing technology to melt the two connecting parts to achieve the actual connection effect. However, in the welding process of 304 stainless steel pipes, defects are caused in the welding parts of 304 stainless steel pipes due to the influence of various factors such as technicians, equipment, materials, welding methods, and natural environment. The internal defects of 304 stainless steel pipe welding include cracks, pores, slag inclusions, incomplete penetration, etc. What are the defects of 304 stainless steel pipe electric welding ?
What are the Disadvantages of 304 Stainless Steel Pipes Electric Welding?
1. Incomplete penetration
Lack of penetration means that there may be continuous or intermittent grooves on the weld surface.Weak specifications, thin electrodes, improper rod delivery, etc. can all lead to incomplete welding. It also weakens the weld, which can easily lead to stress in the enterprise. At the same time, due to the weak social norms in my country, the cooling rate continues to increase, which can easily cause pores, cracks, etc.
2. Stomata
The gases in the molten pool cannot escape until the metal solidifies and remain in the cavity formed in the weld.The gas may be absorbed by the molten pool from the outside, or it may be generated by reaction during the welding metallurgical management process. The main reasons for the occurrence of pores are rust, oil stains on the surface of the base material or the filling metal material, and the welding rod and flux are not baked, which will increase the amount of pores. Because rust, oil, welding rod coating and moisture in the flux decompose into gas under high temperature, the high temperature and the gas content in the metal increase.
The welding line has too little energy and the cooling speed of the molten pool is too high, which is not conducive to improving gas escape. Insufficient deoxidation of the weld metal also increases oxygen porosity. Porosity reduces the effective cross-sectional area of the weld, causing the weld to loosen, thereby reducing the strength and plasticity of a joint and causing leakage. Porosity is also a factor that causes stress concentration. Hydrogen pores may also promote cold cracking.
3. Slag inclusion
The slag remaining in the weld after welding is called slag inclusion. Slag inclusion is a type of solid inclusion defect, which is the slag remaining in the weld. Slag inclusions reduce the plasticity and toughness of the weld.
4. Unfused
The bonding surface or interlayer comparison between the cladding layer and the base material is prone to poor fusion. This is because the sintered flux must be lighter than the smelting flux cladding. Therefore, its melting depth is relatively small. During operation, if the operation is not standardized or the welding parameters are not well controlled, it is more likely to cause surface non-fusion of the joint or interlayer non-fusion defects.
5. Crack
Cold crack: Cracks that occur during the welding process when the welded joint is cooled to a lower ambient temperature are called cold cracks. The main contents of welding cold cracks are distributed under the weld, at the root of the weld and at the weld toe. They have the characteristics of intergranular and transgranular fracture behavior, and the fracture is bright and metallic. Welding cold cracks include quenching embrittlement cracks, delayed cracks, and low-plasticity embrittlement cracks.
Thermal cracks: It refers to crystallization at high temperature and cracks along the grains, also known as crystallization cracks. This type of crack can be observed under an electron microscope. It has the characteristics of intergranular damage. The crack sections of most companies have different oxidation colors. Thermal cracks mainly occur in welds with more impurities and single-phase austenite welds, and sometimes appear in the heat-affected zone. There are vertical and horizontal.
Reheat crack: It means that in order to eliminate the residual stress after welding and improve the metallographic structure and mechanical system performance of the joint, cracks will be generated during the heat treatment process to effectively eliminate different stresses.
Read more: How to ldentify the Quality of 304 Stainless Steel pipes?