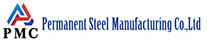
Los tubos de acero inoxidable 304 están hechos de una aleación de acero inoxidable austenítico versátil que contiene cromo (18 %) y níquel (8 %). Esta composición proporciona una excelente resistencia a la corrosión, alta resistencia y buenas características de fabricación.
Tipos de tuberías de acero inoxidable 304:
Sin costura: se fabrican sin costura y se utilizan normalmente para aplicaciones de alta presión.
Soldadas: se crean soldando dos bordes entre sí, son adecuadas para aplicaciones de menor presión.
El método de conexión de soldadura de la tubería de acero inoxidable 304 es utilizar la tecnología de procesamiento de fusión en caliente para fundir las dos partes de conexión para lograr el efecto de conexión real. Sin embargo, en el proceso de soldadura de tuberías de acero inoxidable 304, se producen defectos en las partes de soldadura de las tuberías de acero inoxidable 304 debido a la influencia de varios factores como técnicos, equipos, materiales, métodos de soldadura y entorno natural. Los defectos internos de la soldadura de tuberías de acero inoxidable 304 incluyen grietas, poros, inclusiones de escoria, penetración incompleta, etc. ¿Cuáles son los defectos de la soldadura eléctrica de tuberías de acero inoxidable 304?
¿Cuáles son las desventajas de la soldadura eléctrica de tuberías de acero inoxidable 304?
1. Penetración incompleta
La falta de penetración significa que pueden aparecer ranuras continuas o intermitentes en la superficie de la soldadura. Las especificaciones deficientes, los electrodos delgados, la entrega incorrecta de la varilla, etc. pueden provocar una soldadura incompleta. También debilitan la soldadura, lo que puede generar fácilmente estrés en la empresa. Al mismo tiempo, debido a las débiles normas sociales en mi país, la velocidad de enfriamiento continúa aumentando, lo que puede causar fácilmente poros, grietas, etc.
2. Estomas
Los gases del baño de fusión no pueden escapar hasta que el metal se solidifique y permanezcan en la cavidad formada en la soldadura. El gas puede ser absorbido por el baño de fusión desde el exterior o puede generarse por reacción durante el proceso de gestión metalúrgica de la soldadura. Las principales razones de la aparición de poros son el óxido, las manchas de aceite en la superficie del material base o el material metálico de relleno, y la varilla de soldadura y el fundente no se hornean, lo que aumentará la cantidad de poros. Debido a que el óxido, el aceite, el revestimiento de la varilla de soldadura y la humedad en el fundente se descomponen en gas a alta temperatura, la temperatura alta y el contenido de gas en el metal aumentan.
La línea de soldadura tiene muy poca energía y la velocidad de enfriamiento del baño de fusión es demasiado alta, lo que no favorece la mejora del escape de gas. La desoxidación insuficiente del metal de soldadura también aumenta la porosidad de oxígeno. La porosidad reduce el área transversal efectiva de la soldadura, lo que hace que la soldadura se afloje, reduciendo así la resistencia y la plasticidad de una unión y provocando fugas. La porosidad también es un factor que provoca la concentración de tensiones. Los poros de hidrógeno también pueden favorecer el agrietamiento en frío.
3. Inclusión de escoria
La escoria que queda en la soldadura después de soldar se denomina inclusión de escoria. La inclusión de escoria es un tipo de defecto de inclusión sólida, que es la escoria que queda en la soldadura. Las inclusiones de escoria reducen la plasticidad y la tenacidad de la soldadura.
4. Sin fusión
La superficie de unión o la comparación entre capas entre la capa de revestimiento y el material base es propensa a una fusión deficiente. Esto se debe a que el fundente sinterizado debe ser más ligero que el fundente de fundición del revestimiento. Por lo tanto, su profundidad de fusión es relativamente pequeña. Durante la operación, si la operación no está estandarizada o los parámetros de soldadura no están bien controlados, es más probable que se produzca una falta de fusión en la superficie de la unión o defectos de falta de fusión entre capas.
5. Grietas
Grietas frías: Las grietas que se producen durante el proceso de soldadura cuando la junta soldada se enfría a una temperatura ambiente más baja se denominan grietas frías. El contenido principal de las grietas frías de soldadura se distribuye debajo de la soldadura, en la raíz de la soldadura y en la punta de la soldadura. Tienen las características de comportamiento de fractura intergranular y transgranular, y la fractura es brillante y metálica. Las grietas frías de soldadura incluyen grietas de fragilización por temple, grietas retardadas y grietas de fragilización de baja plasticidad.
Grietas térmicas: Se refiere a la cristalización a alta temperatura y grietas a lo largo de los granos, también conocidas como grietas de cristalización. Este tipo de grieta se puede observar con un microscopio electrónico. Tiene las características de daño intergranular. Las secciones de grietas de la mayoría de las empresas tienen diferentes colores de oxidación. Las grietas térmicas se producen principalmente en soldaduras con más impurezas y soldaduras de austenita monofásica, y a veces aparecen en la zona afectada por el calor. Hay verticales y horizontales.
Grieta por recalentamiento: significa que para eliminar la tensión residual después de la soldadura y mejorar la estructura metalográfica y el rendimiento del sistema mecánico de la unión, se generarán grietas durante el proceso de tratamiento térmico para eliminar eficazmente diferentes tensiones.
Leer más: ¿Cómo identificar la calidad de las tuberías de acero inoxidable 304?