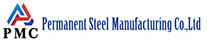
Galvanized steel pipe has the dual advantages of corrosion resistance and long service life, and the price is relatively low, so its usage rate is getting higher and higher. However, some users do not pay attention when welding galvanized pipes, which leads to some unnecessary troubles. So what problems should be paid attention to when welding galvanized pipes?
The prerequisite is to polish
The galvanized layer at the welding point must be polished off, otherwise bubbles, sand holes, false welding, etc. will occur. It will also make the weld brittle and reduce rigidity.
Welding characteristics of galvanized steel pipes
Galvanized steel pipes are generally made by coating a layer of zinc on low carbon steel. The zinc coating is generally 20um thick. The melting point of zinc is 419°C and the boiling point is around 908°C. During welding, zinc melts into liquid and floats on the surface of the molten pool or at the root of the weld. Zinc has a large solid solubility in iron. The liquid zinc will deeply corrode the weld metal along the grain boundaries, and the low-melting-point zinc will form "liquid metal embrittlement". At the same time, zinc and iron can form intermetallic brittle compounds. These brittle phases reduce the plasticity of the weld metal and cause cracks under tensile stress. If the fillet weld is welded, especially the fillet weld of the T-joint, it is most likely to produce through cracks.
When galvanized steel is welded, the zinc layer on the groove surface and edge will oxidize, melt, evaporate and emit white smoke and steam under the action of arc heat, which can easily cause weld porosity. The ZnO formed by oxidation has a high melting point, about 1800°C or above. If the parameters are too small during the welding process, ZnO slag inclusion will occur. At the same time, since Zn becomes a deoxidizer, FeO-MnO or FeO-MnO-SiO2 low melting point oxide inclusions are produced. Secondly, due to the evaporation of zinc, a large amount of white smoke is volatilized, which is irritating and harmful to the human body. Therefore, the galvanized layer at the welding point must be polished off.
Welding process control
The preparation before welding of galvanized steel is the same as that of ordinary low carbon steel. It is important to carefully handle the groove size and the nearby galvanized layer. In order to weld through, the groove size should be appropriate, generally 60~65°, and a certain gap should be left, generally 1.5~2.5mm. In order to reduce the penetration of zinc into the weld, the galvanized layer in the groove can be removed before welding.
In actual work, the centralized beveling process without leaving blunt edges is used for centralized control, and the two-layer welding process reduces the possibility of incomplete welding. The welding rod should be selected according to the base material of the galvanized steel pipe. Generally, J422 is more commonly used for low carbon steel due to its ease of operation.
Welding technique: When welding the first layer of multi-layer welds, try to melt the zinc layer and make it vaporize and evaporate to escape from the weld, which can greatly reduce the amount of liquid zinc left in the weld. When welding fillet welds, try to melt the zinc layer in the first layer and make it vaporize and evaporate to escape from the weld. The method is to first move the end of the electrode forward about 5 to 7 mm, and then return to the original position and continue welding forward after the zinc layer is melted. When welding horizontally or vertically, if short slag electrodes such as J427 are used, the undercut tendency will be very small. If the back and forth wire feeding technology is adopted, defect-free welding quality can be obtained.
Welding of galvanized pipes should pay attention to:
1. Galvanized steel pipes with a diameter greater than 100mm should be connected with flanges or special ferrule fittings.
2. In order to ensure the welding quality, the galvanized weld joints should be treated with galvanized steel pipes and flanges. The galvanized layer should be cleaned with hand grinding wheel or sandpaper, or with gas welding flame.
3. The welding point between galvanized steel pipe and flange should be galvanized for the second time.
Measures to ensure welding quality are:
1. Human factors are the key to control welding of gas galvanized pipes. Due to the lack of necessary post-welding control measures, it is very easy to cut corners and affect quality. At the same time, the welding characteristics of galvanized pipes make it difficult to ensure welding quality. Therefore, before the project starts, skilled welders who hold corresponding boiler pressure vessel or equivalent welder certificates should be selected, necessary technical training and briefing should be carried out, and after on-site welder assessment and approval in accordance with the boiler pressure vessel welder examination rules, permission to enter the site for welding should be granted. The welders should not be replaced at will to ensure that the welders for welding the pipeline are relatively stable.
2. Control of welding materials: ensure that the welding materials purchased are from regular channels, have quality assurance and certificates, and meet the process requirements. The welding machine must have a qualified current and voltage meter to ensure the correct implementation of the welding process. The welding cable cannot be too long. If it is too long, the welding parameters should be adjusted.
3. Welding machine: The welding machine is a welding tool, which must have reliable performance and meet the process requirements; the welding machine must have a qualified current and voltage meter to ensure the correct implementation of the welding process. The welding cable cannot be too long, and the welding parameters must be adjusted if it is too long.
4. Welding process method: ensure the strict implementation of special operation methods for galvanized pipes, conduct pre-welding groove inspection according to welding process, control welding process parameters and operation techniques, and post-welding appearance quality inspection. If necessary, add post-welding non-destructive testing. Control welding layers and the amount of welding materials for each pass.
5. Welding environment control: Ensure that the temperature, humidity and wind speed during welding meet the process requirements. Welding shall not be carried out if the conditions are not met.
Read more: Advantages and Disadvantages of Galvanized Steel Pipe