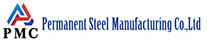
1. Ultrasonic testing
When ultrasonic waves are spread in the tested raw materials, the acoustic characteristics of the raw materials and the changes in the internal organization have a positive impact on the spread of the ultrasonic waves. After detecting the affected levels and conditions of the ultrasonic waves, the changes in the function and structure of the raw materials are understood .
2. Radiographic inspection
Radiographic inspection uses the difference in the amount of radiation transmitted between the normal part and the defective part to form the resolution of the blackness on the negative.
3. Penetrant test
Penetrant test is to use the capillary action of liquid to permeate the penetrant into the opening on the surface of the solid raw material, and then draw the penetrant penetrant to the surface through the developer to show the existence of the defect. Penetration testing is suitable for a variety of metal and ceramic workpieces, and the time from penetration manipulation to the appearance of defects is relatively short, usually about half an hour. It may be useful to detect surface fatigue, stress corrosion and welding cracks, and to directly measure the size of cracks.
4. Magnetic particle detection
Magnetic particle detection is to use magnetic flux leakage to absorb magnetic particles and form magnetic marks to provide defect manifestation. It can detect surface and subsurface defects. The nature of defects is easy to distinguish. Paint and electroplated surfaces do not affect the detection vividness.
5. Eddy current detection
If the eddy current detection mainly uses the eddy current induced in the workpiece by the ferromagnetic coil to analyze the internal quality of the workpiece, it can detect the shortcomings of the surface and near surface of various conductive raw materials, the usual parameter control is troublesome, and the detection results are difficult to explain. Moreover, it is required that the detection object must be a conductive crack, and the length of the fault can be measured euphemistically.
6. Magnetic flux leakage detection
Magnetic flux leakage detection of petroleum casing is based on the characteristics of high permeability of ferromagnetic materials. Basically, the quality of in-service petroleum casing is tested by measuring the permeability change caused by defects in ferromagnetic materials .
7. Magnetic impression detection
Magnetic impression detection is derived from the relationship between the physical nature of the magnetic phenomenon of metals and the dislocation process. It has many advantages such as high utilization, low cost, and no grinding. It has an important and ordinary application prospect in the industry.