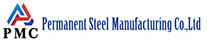
Petroleum casing manufacturers have learned that at present, controlled rolling and controlled cooling technologies have been successfully applied to the production of structural steel such as steel plates and strips, and seamless steel pipes have complex and special existing shapes and complex heat treatment processes. Mill cold control technology is not widely used in industrial production. The results showon-line normalization and on-line accelerated cooling of steel tubes for petroleum casing are the two main ways to achieve steel rolling cooling.
On-line normalization refers to cooling the steel pipe to the transformation point J C1 before rolling, and the steel pipe is transformed from austenite to ferrite, so that the steel pipe enters the heating furnace for a phase change before the heating furnace is reheated, and then reheats the After heating and recrystallization, the grains of the normalizing tube are refined. On-line accelerated cooling is to pass the transformation austenite obtained by controlled rolling through the transformation zone of 750-500 ° C at a typical cooling rate of about 10-50'C / s below the austenite non-recrystallization temperature (7hr) The microstructure is refined to significantly improve strength and toughness.
By controlling the rolling cooling technology, the on-line heat treatment of petroleum casing is realized, which replaces the quenching and tempering treatment after hot rolling, improves the production efficiency, reduces the production cost, and has good application prospects. Under the two technologies of online normalization and online accelerated cooling, the structure and performance of petroleum casing have been greatly improved.