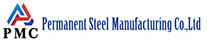
Seamless steel tubes are widely used in the construction field due to their high strength and good toughness. However, seamless pipes may suffer from corrosion in specific construction environments, which will not only reduce their service life but also may cause safety hazards. Therefore, it is very important to take effective anti-corrosion measures. The following summarizes the main methods of preventing corrosion of seamless steel tubes in construction.
The main methods to prevent corrosion of seamless steel tubes
1. Choose corrosion-resistant materials
Alloy steel: Adding alloy elements such as chromium, nickel, and molybdenum can improve the corrosion resistance of steel. For example, stainless steel is a commonly used corrosion-resistant material. Different grades of stainless steel can be selected according to different usage environments.
Weathering steel: This type of steel forms a dense oxide layer on the surface that prevents further corrosion of the internal metal and is suitable for building structures exposed to the natural environment.
Manganese steel, silicon steel: Some studies have shown that elements such as manganese and silicon can improve the oxidation resistance and corrosion resistance of steel.
2. Surface treatment
Coating protection: A protective layer is applied on the surface of the steel pipe to isolate it from the corrosive medium. Paint coatings are low-cost and easy to apply, but their protective effect is limited and requires regular maintenance. Epoxy coating has excellent corrosion resistance, adhesion and wear resistance, suitable for harsh environments. The zinc-rich coating protects the steel through electrochemical protection, sacrificing zinc, and can provide protection even if the coating is scratched. Ceramic coating has extremely high hardness and wear resistance, as well as excellent high temperature resistance and corrosion resistance.
Coating protection: A layer of metal is plated on the surface of the steel pipe to form a protective layer. Common coatings include zinc plating and chrome plating.
Phosphating treatment: A layer of phosphate conversion film is formed on the surface of the steel pipe to improve the adhesion of the coating and enhance the anti-corrosion performance.
3. Environmental Control
Control humidity: Keeping the interior of the building dry and lowering the humidity in the air can reduce corrosion of steel.
Ventilation: Good ventilation can remove moist air and corrosive gases, reducing the risk of corrosion.
Avoid water accumulation: During the design and construction process, water accumulation around the steel structure should be avoided to prevent localized corrosion.
4. Electrochemical protection
Cathodic protection: The steel structure is protected by applying an external current or connecting a sacrificial anode, making it a cathode. This method is suitable for buried or underwater steel structures.
5. Construction and maintenance
Standardized construction: During the construction process, damage to the protective layer of the steel pipe should be avoided and any damage should be repaired in time.
Regular inspection and maintenance: Regularly inspect steel structures for corrosion and perform maintenance and repairs as needed, such as repainting or replacing severely corroded parts.
Anti-corrosion measures for different environments
1. General environment: Simple anti-corrosion measures such as paint coating or galvanizing can be adopted.
2. Wet Environments: Corrosion-resistant materials such as epoxy coating, zinc-rich coating or stainless steel are recommended.
3. Marine environment: Higher level anti-corrosion measures are required, such as heavy anti-corrosion coating, cathodic protection, etc.
4. High temperature environment: It is necessary to consider issues such as high temperature oxidation and creep, and select high temperature resistant alloy steel or ceramic coating. Seamless steel pipes for transporting high temperature gas need to be insulated to prevent heat loss of the gas.