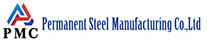
Stainless steel seamless pipe is a long stainless steel pipe with a hollow cross-section and no seams around it. It is made of solid stainless steel billet through a series of complex processes such as perforation, hot rolling, and cold rolling. The entire pipe has no traces of welding and the pipe wall is complete and continuous. Stainless steel pipes also have some common defects. Let's take a closer look.
1. External fold
Characteristics: spiral layered folds on the outer surface of the steel pipe.
Causes:
1) There are folds or cracks on the surface of the tube.
2) The subcutaneous pores and subcutaneous inclusions of the tube are serious.
3) The surface of the tube is not cleaned well or has ears, misalignment, etc.
4) During the rolling process, the surface of the steel pipe is lifted and scratched, and then pressed onto the base of the steel pipe through rolling, forming external folds, etc.
Inspection: Not allowed: Minor cases can be repaired, and the actual values of the wall thickness and outer diameter after grinding shall not be less than the minimum values required by the standard.
2. Delamination
Characteristics: Spiral or block-shaped delamination and cracking on the surface of the steel pipe.
Causes: Severe non-metallic inclusions in the tube blank, residual shrinkage or severe looseness, etc.
Inspection: Not allowed to exist.
3. External scars
Characteristics: The outer surface of the steel pipe shows scars.
Causes:
1) The rollers are sticky, aged, severely worn or rubbed.
2) The conveyor rollers are sticky with foreign matter or severely worn.
Inspection:
1) External scars distributed in pieces should be ground or removed.
2) On the pipe section with external scars, the area of external scars exceeding 10% should be removed or ground.
3) External scars with a depth exceeding 5% of the wall thickness should be ground.
4) The actual values of the wall thickness and outer diameter at the grinding point shall not be less than the minimum value required by the standard.
4. Net-like cracks
Characteristics: Small fish-scale cracks with large pitch and band-like shape appear on the outer surface of the steel pipe.
Causes:
1) Too high harmful element content in the tube (such as arsenic).
2) Aging and steel sticking of the perforating roller.
3) Steel sticking of the guide plate, etc.
Inspection: It should be completely removed. The actual values of the wall thickness and outer diameter after removal shall not be less than the minimum value required by the standard.
Size out of tolerance
1. Uneven wall thickness
Characteristics: The wall thickness of the steel pipe is uneven on the same section, and the wall thickness and the small wall thickness are very different.
Causes:
1) Uneven heating of the tube.
2) The rolling line of the piercing machine is not adjusted, and the centering roller is unstable.
3) The head is worn or the back hole of the head is eccentric.
4) Correction of the centering hole of the tube.
5) The curvature and cutting slope of the tube are too large.
Inspection: Measure each tube, and the uneven wall thickness end should be cut off.
2. Wall thickness tolerance
Characteristics: The wall thickness of the steel pipe exceeds tolerance in one direction. The one exceeding positive deviation is called excessive wall thickness; the one exceeding negative deviation is called excessive wall thickness.
Causes:
1) Uneven heating of the tube blank.
2) Improper adjustment of the punching machine.
Inspection: Measure each tube, the end that exceeds tolerance should be cut off, and the full length that exceeds tolerance should be revised or scrapped.
3. Outer diameter tolerance
Characteristics: The outer diameter of the steel pipe exceeds the standard. The one that exceeds the positive tolerance is called the outer diameter is large, and the one that exceeds the negative tolerance is called the outer diameter is small.
Causes:
1) The hole type of the sizing machine is too worn, or the new hole type design is not reasonable.
2) The final rolling temperature is unstable.
Inspection: Measure each pipe, and the one that exceeds the standard should be revised or scrapped.
4. Bending
Features: The steel pipe is not straight along the length direction or the bend at the end of the steel pipe is called "goose head bend".
Causes:
1) Local water cooling during manual heat inspection.
2) Improper adjustment during straightening, serious wear of straightening roller.
3) Improper processing, assembly and adjustment of sizing machine.
4) Bending caused by lifting and transportation.
Inspection: When the bending exceeds the standard, it can be straightened twice, otherwise it will be scrapped. "Goose head bend" that cannot be straightened should be removed.
5. Length Exceeds the Requirement
Characteristics: The length of the steel pipe exceeds the requirement. The excess positive difference is called long length, and the excess negative difference is called short length.
Causes:
1) The length of the tube exceeds the standard.
2) Unstable rolling.
3) Poor control during slitting, etc.
Inspection: Long tubes are cut again or re-judged, and short tubes are re-judged or scrapped
Read more: Inner Surface Defects of Stainless Steel Seamless Pipes