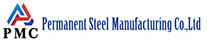
4) Avoid the Mn/Si ratio in the chemical composition of the steel strip being less than 8:1 (avoid less than 4:1 when the impact toughness requirement is low)
2. Pre-arc
This defect is actually caused by insufficient fusion caused by the pre-arc. Usually, the burrs, oxide skin and rust on the edge of the strip form a bridge before the vertex of the V angle, causing the short-circuit to cause the current to jump and produce a pre-arc phenomenon. The short-circuit current changes the current direction and reduces the heat at the V corner.
Precaution:
1) The V-shaped angle is strictly controlled at 4 ~ 6;
2) The strip edge is clean, smooth and free of burrs;
3) Keep the cooling water clean, control the flow direction of the cooling water, and try to avoid the flow to the V angle.
3. Insufficient fusion
This defect is due to the fact that the edges of the two strips are heated but not fully fused, and a good weld is not formed. The direct reason for the lack of fusion is the lack of heat during welding. There are many related factors that lead to insufficient welding heat, such as high-frequency power. Output, V angle and heating length, position of magnet bar, working condition and cooling of magnet bar, size of induction coil, welding speed, etc., these factors influence each other, and the combined effect leads to such defects.
Precaution:
1) The matching of welding input heat and welding speed, and the characteristics of the raw material of the tube blank
2) The position of the magnet bar exceeds the center of the squeeze roller by 1/8 in (3.18 mm);
3) The length of the V-shaped opening angle does not exceed the length of the pipe diameter;
4) The angle of the V-shaped mouth does not exceed 7 degrees;
5) The difference between the inner diameter of the induction coil and the outer diameter of the steel pipe is not more than 1/4 in (6.35 mm);
6) The width of the steel strip is suitable and meets the requirements of the production pipe diameter.
Read more: Seamless vs ERW Welded pipe