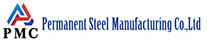
In order to ensure the quality of welding, the processing of the workpiece that needs to be welded before welding can be gas cutting or cutting. Generally, it is a bevel, and sometimes it is a curved surface. For example, two steel plates with a thickness of 10mm are to be butt welded together. For a firm weld, a chamfer is milled on the edge of the plate. This is called beveling. Due to the difference in material thickness and welding quality requirements, the welding joint and groove shape are also different. Generally, the groove forms are divided into K-type, V-type, I-type, U-type, X-type, etc.
The fillet radius at the bottom of the J-shaped and U-shaped groove is called the root radius. Its function is to increase the space at the root of the groove so as to penetrate the root.
Function:
The main function of the groove is to ensure the penetration of the root of the weld, so that the welding heat source can penetrate into the root of the joint to ensure the quality of the joint. At the same time, the groove can also play a role in adjusting the ratio of base metal to filler metal.
(6) Selection of welding groove
The selection of welding groove generally follows the following principles:
① It can ensure the penetration of the workpiece (the penetration depth of manual arc welding is generally 2 ~ 4mm), and it is convenient for welding operation. If the inside of the container is inconvenient for welding, a single-sided groove should be used to weld on the outside of the container.
② The groove shape should be easy to process.
③ Improve welding productivity and save welding rods as much as possible.
④ Minimize the deformation of the workpiece after welding as much as possible.
Groove welding symbols:
A groove weld will be used when to parts come together in the same plane. These welds will be applied in a butt joint and may have a preparation or not before welding. This is the reason there are several types of groove welding symbols.
The symbols for these grooves are nearly identical to the symbols that represent them.
Tips: ERW welded pipe is formed by rolling strip and welding the seam, with tighter dimensional tolerances and less weight. The weld seam is heat treated after welding that no untempered martensite remains, and the weld flash can be removed from both inner and outer surfaces.