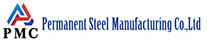
High-frequency welding (ERW Pipe) machine welding uses the unique skin effect and proximity effect of high-frequency current, so that the welding current is concentrated on the surface of the contact, the temperature of the surface joint surface rises rapidly, and the surface to be welded is heated to a plastic state of melting or near melting. A pressure welding method that is then quickly extruded into a joint. This welding method has a series of advantages: the weld heat affected zone is small, the heating speed is fast, so the welding speed and weld quality of the frequency welder can be greatly improved, and the strip steel which is not pickled, shot blasted and trimmed can be used as the blank. At the same time, it can weld alloy steel, high alloy steel and non-ferrous metal pipe, which greatly reduces the unit power consumption. A variety of metal welded pipes can be produced with a single welding equipment. For different metals, only the welding power and welding speed have to be changed accordingly.
The advantages of contact type high frequency welding machine welding are:
1) Less effective splitting;
2) High current density and high efficiency due to the proximity of the contact head;
3) Small thermal influence range;
4) Small influence of pipe diameter, weldable pipes with a diameter of about 8 to 1270 mm;
5) Welding speeds of up to 100 to 120 m/min. Such high welding speeds and beveled metal layers make it possible to weld light alloys, stainless steel, copper, brass and zirconium without protection. And other metal pipes.
The disadvantages are: 1) Consumption of the contact head; 2) Erosion defects; 3) Small heating range, rapid burning, which is unfavorable to the inner surface of the tube.
The advantages and disadvantages of induction welding are contrary to the above, especially the influence of the pipe diameter. In production practice, induction welding methods are often chosen. This is because induction welding has the following significant advantages over contact welding:
1) Fundamentally eliminates equipment failure caused by open circuit, thereby improving equipment utilization and reducing production costs;
2) Welding process is stable, welding Good quality, smooth surface of welds;
3) Less stringent requirements on strip joints and surface quality, thus reducing labor intensity;
4) Most suitable for welding thin-walled tubes due to electrodeless pressure;
5) No contact electrode consumption, thus it saves non-ferrous metals and saves downtime caused by electrode replacement;
6) Welding adjustment is easy and convenient. However, the power required for induction welding is 40 to 50% higher than that required for contact welding. When the power of the welding device is the same as that of the welded pipe, the induction welding speed is 1/2 to 2/3 of the contact welding speed.
Read more: What is HFW steel pipe?