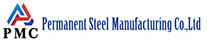
They are the most common type of carbon steel pipe used in industry today and they are very similar. While the differences between the A106 and A53 are minor, they matter a great deal in terms of when and where each is specified. Let’s introduce them.
A106 vs. A53-welded vs. seamless steel pipe
The most important difference is that pipe that meets the A106 standard must be seamless, while pipe that meets the A53 standard can be seamless or welded.
Welded pipe, also known as welded steel pipe, is basically a steel pipe made of steel plates or strips that are welded after being curled and formed.
Seamless pipes are made by piercing fiber optic steel strips through the middle while hot, creating the same shape but without seams
Differences in application
A106 pipe application:
A106 pipe is designed for high temperature and high pressure applications and is commonly used in power generation applications. High-pressure, high-heat use environments can put additional pressure on pipes, so in these environments, seamless pipe types are preferred because they’re at less risk of failure under stress than their welded counterparts.
A53 pipe application:
1. Construction, underground transportation, extraction of ground water while building, steam water transportation etc.
2. Bearing sets, machinery parts processing.
3. Electric application: Gas transmission, water power generation fluid pipeline.
4. Wind power plant anti-static tube etc.
5. Pipelines that required zinc coated.
Differences in chemical makeup
In addition to the way the A106 and A53 standards dictate pipe manufacture, the standards feature slight differences in chemical makeup. The most significant difference is that the A106 tube contains silicon, while the A53 tube does not.
Silicon acts as an alloying element to increase the heat resistance of A106 pipe, which is suitable for high-temperature applications. Without it, regular exposure to high temperatures can weaken pipes over time, increasing the risk of failure.
The A106 and A53 standards also contain varying amounts of sulfur and phosphorus, depending on the grade. These elements are normally considered impurities in steel, so their incorporation in piping is minimal. However, the trace amounts of these elements add machinability to steel pipe.