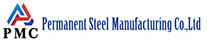
What is non-destructive testing?
Non-destructive testing, referred to as NDT, is a modern inspection technology that detects the shape, position, size and development trend of internal or external defects without damaging the object to be inspected. It has been widely used in steel pipe production in recent years. The non-destructive testing methods used in the production of seamless pipes mainly include magnetic particle testing, ultrasonic testing, eddy current testing, radiographic testing, penetrant testing, etc., and various testing methods have a certain range of application.
For the defects of seamless steel pipes, magnetic flux leakage detection method, ultrasonic detection method, eddy current flaw detection method, etc. can be used.
The magnetic flux leakage detection method is to use the magnetic flux leakage principle to detect the seamless steel pipe. During the inspection process, the inspected seamless steel pipe should be magnetized first, because the surface of the inspected seamless steel pipe will only have a magnetic leakage field after magnetization. This detection method uses the sensor to obtain the leakage magnetic field information. Therefore, this method is especially suitable for automatic flaw detection, which can detect a large number of seamless steel pipes in a short time.
The detection method has certain limitations in the use process, and a detection blind zone will appear at the end of the seamless steel pipe during detection, and the length of the detection blind zone is about 200mm. The main form of the testing equipment is a point probe and a through probe. Among them, the point probe moves forward in a spiral form during detection, but the detection efficiency is low and the inspection time is long. The penetrating probe not only has simple inspection equipment, fast inspection speed, but also has high sensitivity. Therefore, the eddy current testing method is the most widely used.
Extended information:
What are the performance tests for seamless steel pipes?
1. Hydraulic test
The tested seamless steel pipe was filled with water under a certain working pressure. And keep it under the working pressure for a certain period of time (the working pressure value of the test and the time of the voltage stabilizer tube are determined according to the specification), and there is no leakage. Experimentation is a high-quality test that is often used for full inspection of a product.
2. Tensile test
Put the seamless steel pipe test piece on the bending test machine, and bend it to the angle specified by the specification according to the standard bending core, and there is no crack or crack on the surface of the bending part.
3. Flattening test
The seamless steel pipe test piece is placed between two tablet computer fixtures, and a force is applied between the fixtures to make the interval exceed the standard value, and the deformation area of the test piece is checked for defects such as gaps and cracks.
4. Flaring test
During the flaring test, place the seamless steel pipe specimen on the workbench with the opening facing up. Press the jacking center with standard taper into the seamless steel tube. Until the expansion ratio of the test diameter exceeds the standard, there is no crack on the surface of the test piece.