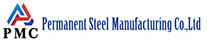
Hot-rolled seamless steel pipe is one of the important production types of seamless steel pipe. It is made of round steel billet as raw material, after high temperature heating, through perforation, rolling and other processes. Because the metal is in a thermoplastic state during production, internal defects can be eliminated, making the pipe structure denser. Hot rolled seamless steel pipes have some unique requirements when welding compared to other types of steel pipes. The welding quality directly affects the overall strength, durability and long-term performance of the steel pipe. In order to ensure the smooth progress of the welding process and the quality of the welded joints, the following key requirements need to be met:
Preparation before welding
Preheating treatment: For thicker hot-rolled seamless steel pipes, especially alloy steel or high carbon steel pipes, preheating treatment is usually required before welding. Preheating can reduce thermal cracks caused by excessive temperature gradient during welding, and reduce the cooling rate of the welding area to prevent the occurrence of welding defects.
Design of welding joints: In the welding process of hot-rolled seamless steel pipes, the design of the joints is crucial. Choosing the appropriate joint shape, size and angle, as well as the correct groove design, can ensure uniform stress distribution during welding, reduce stress concentration and improve welding strength.
Selection of welding process
Welding method: Common welding methods include manual arc welding (SMAW), gas shielded welding (MIG welding), argon arc welding (TIG welding), etc. Choose the right welder according to the material, wall thickness and application environment of the hot-rolled seamless steel pipe. For thick-walled steel pipes, gas shielded welding (MIG) or argon arc welding (TIG) is usually recommended because these welding methods can provide better welding quality.
Welding parameters: Welding current, welding voltage, welding speed and other parameters need to be adjusted according to the thickness, material and required welding quality of the steel pipe. Too high welding current may cause overheating of the welding area, resulting in deformation of the steel pipe, welding cracks and other problems; too low current may lead to insufficient welding and affect the strength of the joint.
Heat treatment requirements
Heat treatment after welding: A large heat-affected zone will be generated during welding, and the mechanical properties and organizational structure of this area will usually change. Appropriate heat treatment, such as annealing, normalizing or aging treatment, is required after welding to restore the mechanical properties of the weld zone and eliminate welding residual stress. Especially in the welding of high-strength steel pipes, heat treatment is crucial to ensure the toughness and strength of the joint.
Stress relief: For some special applications (such as oil and gas pipelines, chemical equipment, etc.), the welded steel pipe may need to be stress relieved annealed to reduce the risk of cracking due to stress accumulation during the welding process.
Selection of welding materials
Welding filler material: The selection of welding filler material should match the material of hot-rolled seamless steel pipe to ensure that the mechanical properties of the welded joint are close to those of the parent material. Common filler materials include stainless steel welding rods, alloy steel welding wires, etc. The use of inappropriate filler materials may lead to insufficient strength of the joint or corrosion problems.
Protective gas: In gas shielded welding (MIG, TIG), the protective gas used has a significant impact on the welding quality. Generally, carbon dioxide or argon is used as the protective gas. Carbon dioxide is suitable for welding of common steel, while argon is suitable for high alloy steel or situations where higher welding quality is required.
Post-welding inspection and quality control
Nondestructive testing of welded joints: After welding is completed, nondestructive testing is required to ensure the quality of the welded joints. Commonly used non-destructive testing methods include X-ray inspection, ultrasonic testing, magnetic particle testing and penetration testing, which can effectively detect internal defects in welding, such as pores, cracks, inclusions, etc.
Mechanical properties test: The mechanical properties of the welded joint should be tested, such as tensile test, impact test, hardness test, etc., to ensure that the strength, toughness, plasticity and other indicators of the welded joint meet the design requirements.
Corrosion performance testing: If the steel pipe is used in a highly corrosive environment (such as seawater, chemical media, etc.), the corrosion resistance of the welded joint needs to be tested. Common corrosion testing methods include salt spray test, chloride stress corrosion test, etc.
Welding stress and deformation control
Control welding deformation: Since hot-rolled seamless steel pipes are affected by temperature changes during welding, thermal expansion and contraction during welding may cause deformations such as bending and warping of the steel pipes. In order to control these deformations, the following measures can be taken:
Control the welding sequence: use segmented welding or symmetrical welding to reduce thermal stress accumulation.
Intermittent cooling during welding: When welding in sections, allow the weld zone to fully relax during the cooling process to avoid overheating.
Fixture Fixing: Use a clamp or support device to fix the steel pipe to ensure that the correct geometry is maintained during welding.
Temperature control during welding
Control welding temperature: For hot rolled seamless steel pipes, it is very important to control the temperature of the steel pipe during welding. Too high welding temperature may cause the steel pipe to overheat, resulting in a large heat-affected zone, which in turn affects the welding quality and the mechanical properties of the material. To avoid this, temperature monitoring equipment is needed to control the temperature of the welding area.
Welding cooling control: The cooling rate after welding needs to be properly controlled to avoid thermal cracks or low-temperature brittleness caused by rapid cooling. During the cooling process, the cooling rate can be optimized by controlling the ambient temperature of the weld zone or by using a coolant.
Welding requirements for special material steel pipes
For hot-rolled seamless steel pipes made of special materials such as high alloy steel, corrosion-resistant steel or high-temperature resistant steel, the welding requirements are more stringent. These steel pipes may require the use of specialized welding materials during welding, and the temperature, cooling rate and stress distribution must be strictly controlled during the welding process.
Corrosion-resistant steel pipes (such as stainless steel pipes): During the welding process, it is necessary to avoid the destruction of the passivation film caused by high temperature, which may lead to increased corrosion in the welding area.
Read more: Wide Application of Hot Rolled Seamless Steel Pipes