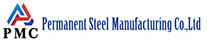
The materials of elbows include cast iron, stainless steel, alloy steel, wrought iron, carbon steel, non-ferrous metals and plastics, etc. The ways to connect with pipes include: direct welding (the most common way), flange connection, hot melt connection, electric fusion connection, threaded connection and socket connection, etc.
Classification of stainless steel elbows
Stainless steel elbows are a common type of pipe connector in the field of industrial pipelines. According to different application scenarios and requirements, stainless steel elbows can be classified according to bending radius, bending angle and connection method. Stainless steel elbows have a wide range of applications and are commonly found in petrochemical, chemical, pharmaceutical, food and other industrial fields.
According to the different bending radius, stainless steel elbows can be divided into long radius elbows and short radius elbows. Long radius elbows have a larger bending radius and are suitable for scenes with a larger bending degree and lower liquid flow velocity requirements. Short radius elbows have a smaller bending radius and are suitable for scenes with a smaller bending degree or where a compact pipeline system is required.
According to the different bending angles, stainless steel elbows can be divided into 45-degree elbows and 90-degree elbows. 45-degree elbows are suitable for scenarios where the pipe needs to be bent at a smaller angle, and 90-degree elbows are suitable for scenarios where the pipe needs to be bent at a right angle.
According to the different connection methods, stainless steel elbows can be divided into welded elbows and threaded elbows. Welded elbows are suitable for scenarios where connections are required, and threaded elbows are suitable for scenarios where frequent disassembly or adjustment is required, and have more flexible application characteristics.
In practical applications, stainless steel elbows are widely used in industrial fields such as petrochemicals, chemicals, pharmaceuticals, and food. They have been optimized in design and material selection, have good corrosion resistance and strength, can meet the requirements of different media and processes, and provide reliable support for the safe operation of industrial pipelines.
What is the manufacturing process of stainless steel elbows?
What are their advantages, disadvantages and applicable scope? The manufacturing process of stainless steel elbows usually includes the following common methods:
1. Hot extrusion forming: This process is to heat the stainless steel billet to a certain temperature, and then use a die on the extruder to extrude the billet into shape, and obtain the elbow shape through processing and trimming. The advantages include high production efficiency, relatively low cost, and suitable for mass production; the disadvantages are that it requires more equipment and consumes more energy. It is suitable for situations with higher cost requirements and larger batches.
2. Cold heading: This process uses pressure equipment to press stainless steel billets into shape at room temperature. The desired elbow shape can be achieved through multiple passes of extrusion and forming. The advantage is that the mechanical properties of the material are less affected during the forming process, and it is suitable for situations where high material performance requirements are required; the disadvantage is that the production efficiency is low. It is suitable for situations where the batch size is small and the material performance requirements are high.
3. Welding manufacturing: After bending the stainless steel pipe, the pipe is connected into an elbow shape through welding process. The welding methods can include manual welding, automatic welding, etc. The advantages are simple process and great flexibility, which can meet the requirements of various shapes and specifications; the disadvantage is that the material may be degenerated and deformed during the welding process. It is suitable for occasions with flexible specifications and high adaptability requirements.
4. Precision casting: This process is to form the stainless steel elbow by casting, which can obtain products with complex shapes and high precision. The advantage is that it can produce elbows with complex structures, with high surface finish, suitable for high precision and complex shape requirements; the disadvantage is that the cost is relatively high. It is suitable for products in the fields of precision instruments, aerospace, etc.
Read more: Types of Elbow Fittings in Piping