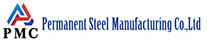
Seamless carbon steel pipe is a weldless pipe made of carbon steel by hot rolling, cold rolling or cold drawing. It is widely used because of its uniform internal structure and high strength. According to the carbon content, it is divided into low carbon steel (≤0.25%), medium carbon steel (0.25%~0.6%), and high carbon steel (>0.6%). It has the characteristics of strong pressure bearing capacity, mature technology and low cost. It is suitable for scenes such as industrial pipelines, mechanical structures, and building pile foundations, but its corrosion resistance is relatively weak and requires protection such as painting and galvanizing. It has various specifications (outer diameter 6mm~630mm) and can be customized according to needs. It is an indispensable pipe in basic industries.
Annealing conditions of seamless carbon steel pipes
1. Heating temperature: Low carbon steel/hypoeutectoid steel should be heated to 30~50℃ above Ac₃ (850~920℃); high carbon steel/hypereutectoid steel should be heated to 20~30℃ above Ac₁ (760~790℃), avoid overheating.
2. Insulation time: calculated according to the wall thickness, usually 0.5~1 hour for every 10mm thickness to ensure uniform heat penetration.
3. Cooling method: Slowly cool to below 500℃ with the furnace and then air cool. High carbon steel needs to be cooled more slowly (≤20℃/h) to prevent the precipitation of network carbides.
4. Special process: Spheroidizing annealing can be used to improve the machinability of medium and high carbon steel, and cold-processed tubes need stress relief annealing (500~650℃).
What are the special requirements for different types of seamless carbon steel pipes during annealing?
Low seamless carbon steel pipes generally have a carbon content of less than 0.25%, such as common 10# and 20# steels. It has good plasticity and weldability and is easy to process and shape. Annealing temperature is usually between 500 and 650°C, which is not too high. The heating rate can be slightly faster because low carbon steel has better uniformity of structure. Rapid heating is also less likely to produce defects and can complete the temperature rise preparation before annealing more efficiently. The holding time is also short, generally 1-2 hours. This is because the carbon atoms in low-carbon steel diffuse faster, and the organization can be homogenized in a shorter time, thereby eliminating internal stress, improving plasticity and toughness, and better meeting the needs of subsequent processing.
Medium seamless carbon steel pipe, with a carbon content between 0.25% and 0.60%, is like the common 45# steel. It is like a power player with high strength and hardness. It is often used in the manufacture of mechanical parts, automotive parts and other fields with high strength requirements. Its annealing requirements are more "precise". The annealing temperature is usually between 650 and 750°C, which is higher than that of low carbon steel to meet the requirements of internal structural transformation of medium carbon steel. The heating speed needs to be moderate. If it is too fast, the steel pipe will deform or even crack due to thermal stress; if it is too slow, the efficiency will be low. The insulation time is relatively long, about 2-3 hours, so that the carbon atoms have enough time to diffuse evenly, fully eliminate internal stress, and homogenize the structure. Cooling speed is also critical. Generally, it is cooled with the furnace or slowly cooled in the air.
High seamless carbon steel pipes, with a carbon content generally greater than 0.60%, are like a tough but slightly "stubborn" craftsman. They have high hardness and good wear resistance, but lack toughness. They are often used to manufacture tools such as knives and molds that have extremely high hardness requirements. The annealing process is like a delicate carving, and every step needs to be carefully controlled.
The annealing process of high carbon steel seamless pipe is relatively complicated, and the common ones are complete annealing, incomplete annealing and spheroidizing annealing.
When fully annealing, it needs to be heated to 30-50℃ above Ac3, generally around 760-780℃, and properly kept warm to allow the structure to be completely austenitized. Then it is slowly cooled, with a furnace cooling rate of about 10-20℃/h, until it cools to 500-600℃ and then air-cooled out of the furnace. The purpose is to refine the grains, make the structure uniform, reduce the hardness, and make subsequent mechanical processing smoother; The heating temperature of incomplete annealing is between Ac1 and Ac3, about 720-740℃. After keeping warm, it is slowly cooled in the furnace, which can reduce the hardness, eliminate internal stress, and retain a certain wear resistance. Spheroidizing annealing requires heating to 20 - 30℃ above Ac1, i.e. 750 - 770℃, keeping the temperature for 3 - 6 hours, cooling at a rate of about 20 - 50℃/h until 500 - 600℃, then air cooling out of the furnace.
Precautions for the whole annealing process
1. Temperature control: The heating temperature should be set strictly according to the type of steel. Hypoeutectoid steel should be heated to 30-50℃ above Ac₃, and eutectoid/hypereutectoid steel should be heated to 30-50℃ above Ac₁ to prevent excessive temperature from causing coarse grains and reduced pipe performance, and avoid thermal stress caused by excessive heating speed.
2. Uniform heating: Ensure uniform temperature in the furnace and place the steel pipes reasonably to avoid local overheating or insufficient heating; for thick-walled pipes or steel pipes with larger diameters, appropriately extend the heating time to ensure consistent temperature inside and outside.
3. Insulation time: Calculate the insulation time based on the wall thickness of the steel pipe, 0.5-1 hour for every 10mm wall thickness to ensure sufficient transformation of the structure; maintain the furnace temperature stable during the insulation period to avoid temperature fluctuations affecting the annealing effect.
4. Cooling management: After annealing, furnace cooling is usually adopted. When the furnace temperature drops below 500℃, it can be air-cooled. The cooling rate of high carbon steel needs to be slower (≤20℃/h) to prevent the precipitation of network carbides. Avoid deformation of steel pipes or generation of new internal stress caused by rapid cooling.
5. Atmosphere protection: To prevent oxidation and decarburization of the steel pipe surface, a protective atmosphere (such as nitrogen, argon) can be used or an anti-oxidation coating can be applied on the steel pipe surface; if ordinary air furnace annealing is used, the surface oxide scale should be cleaned in time after annealing.
6. Equipment and operation: Regularly check the annealing furnace temperature control system, heating elements and other equipment to ensure normal operation; operators must strictly abide by safety regulations and wear protective equipment to prevent burns, electric shock and other accidents.
7. Quality inspection: After annealing, the steel pipe is subjected to hardness test, metallographic structure analysis and other tests to check whether the grain size and structural uniformity meet the requirements; if it is found that the performance does not meet the standards, the reasons need to be analyzed and re-annealing is carried out.
Read more: 10# Seamless Carbon Steel Pipe: Solid Backbone in the Industrial Field