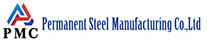
La tubería de acero al carbono sin costura es una tubería sin soldadura fabricada mediante laminación en caliente, laminación en frío o estirado en frío. Es ampliamente utilizada debido a su estructura interna uniforme y alta resistencia. Según su contenido de carbono, se divide en acero de bajo carbono (≤0,25%), acero de carbono medio (0,25%~0,6%) y acero de alto carbono (>0,6%). Se caracteriza por su alta capacidad de carga, tecnología avanzada y bajo costo. Es adecuada para aplicaciones como tuberías industriales, estructuras mecánicas y cimentaciones de pilotes de edificios, pero su resistencia a la corrosión es relativamente baja y requiere protección como pintura y galvanizado. Tiene diversas especificaciones (diámetro exterior de 6 mm a 630 mm) y se puede personalizar según las necesidades. Es una tubería indispensable en las industrias básicas.
Condiciones de recocido de tubos de acero al carbono sin costura
1. Temperatura de calentamiento: El acero de bajo carbono/acero hipoeutectoide debe calentarse a 30-50 °C por encima de Ac₃ (850-920 °C); el acero de alto carbono/acero hipereutectoide debe calentarse a 20-30 °C por encima de Ac₁ (760-790 °C), evitando el sobrecalentamiento.
2. Tiempo de aislamiento: Se calcula según el espesor de la pared, generalmente de 0,5 a 1 hora por cada 10 mm de espesor para asegurar una penetración uniforme del calor.
3. Método de enfriamiento: Enfriar lentamente por debajo de 500 °C en el horno y luego enfriar al aire. El acero de alto carbono debe enfriarse más lentamente (≤20 °C/h) para evitar la precipitación de carburos en la red.
4. Proceso especial: El recocido esferoidizante se puede utilizar para mejorar la maquinabilidad del acero con contenido medio y alto de carbono, y los tubos procesados en frío necesitan un recocido de alivio de tensión (500~650 ℃).
¿Cuáles son los requisitos especiales para los diferentes tipos de tubos de acero al carbono sin costura durante el recocido?
Los tubos de acero sin costura de bajo carbono generalmente tienen un contenido de carbono inferior al 0,25 %, como los aceros comunes de calibre 10# y 20#. Presentan buena plasticidad y soldabilidad, y son fáciles de procesar y conformar. La temperatura de recocido suele estar entre 500 y 650 °C, lo cual no es demasiado alto. La velocidad de calentamiento puede ser ligeramente mayor debido a la mayor uniformidad de estructura del acero de bajo carbono. El calentamiento rápido también reduce la probabilidad de defectos y permite completar la preparación para el aumento de temperatura antes del recocido de forma más eficiente. El tiempo de mantenimiento también es corto, generalmente de 1 a 2 horas. Esto se debe a que los átomos de carbono en el acero de bajo carbono se difunden más rápidamente y la estructura se puede homogeneizar en menos tiempo, eliminando así la tensión interna, mejorando la plasticidad y la tenacidad, y satisfaciendo mejor las necesidades del procesamiento posterior.
Los tubos de acero sin costura de medio carbono, con un contenido de carbono entre el 0,25 % y el 0,60 %, son similares al acero común de calibre 45#. Se caracterizan por su alta resistencia y dureza. Se utiliza a menudo en la fabricación de piezas mecánicas, automotrices y otros campos con altos requisitos de resistencia. Sus requisitos de recocido son más precisos. La temperatura de recocido suele estar entre 650 y 750 °C, superior a la del acero de bajo carbono, para cumplir con los requisitos de transformación estructural interna del acero de medio carbono. La velocidad de calentamiento debe ser moderada. Si es demasiado rápida, la tubería de acero se deformará o incluso se agrietará debido a la tensión térmica; si es demasiado lenta, la eficiencia será baja. El tiempo de aislamiento es relativamente largo, de unas 2 a 3 horas, para que los átomos de carbono tengan tiempo suficiente para difundirse uniformemente, eliminar por completo la tensión interna y homogeneizar la estructura. La velocidad de enfriamiento también es crucial. Generalmente, se enfría en horno o lentamente al aire.
Los tubos de acero sin costura de alto carbono, con un contenido de carbono generalmente superior al 0,60 %, son como un artesano tenaz pero algo obstinado. Presentan alta dureza y buena resistencia al desgaste, pero carecen de tenacidad. Se utilizan a menudo para fabricar herramientas como cuchillos y moldes con requisitos de dureza extremadamente altos. El proceso de recocido es como un tallado delicado, y cada paso debe controlarse cuidadosamente.
El proceso de recocido de los tubos sin costura de acero de alto carbono es relativamente complejo; los más comunes son el recocido completo, el recocido incompleto y el recocido esferoidizante.
Para el recocido completo, es necesario calentarlos a 30-50 °C por encima de Ac3, generalmente alrededor de 760-780 °C, y mantenerlos adecuadamente calientes para permitir que la estructura se austenice por completo. Luego se enfría lentamente, con una velocidad de enfriamiento del horno de aproximadamente 10-20 ℃/h, hasta que se enfría a 500-600 ℃ y luego se enfría al aire fuera del horno. El propósito es refinar los granos, hacer la estructura uniforme, reducir la dureza y hacer que el procesamiento mecánico posterior sea más suave; La temperatura de calentamiento del recocido incompleto está entre Ac1 y Ac3, aproximadamente 720-740 ℃. Después de mantener caliente, se enfría lentamente en el horno, lo que puede reducir la dureza, eliminar la tensión interna y mantener cierta resistencia al desgaste. El recocido esferoidizante requiere calentar a 20-30 ℃ por encima de Ac1, es decir, 750-770 ℃, manteniendo la temperatura durante 3-6 horas, enfriando a una velocidad de aproximadamente 20-50 ℃/h hasta 500-600 ℃, luego enfriando al aire fuera del horno.
Precauciones durante todo el proceso de recocido
1. Control de temperatura: La temperatura de calentamiento debe ajustarse estrictamente según el tipo de acero. El acero hipoeutectoide debe calentarse a 30-50 °C por encima de Ac₃, y el acero eutectoide/hipereutectoide debe calentarse a 30-50 °C por encima de Ac₁ para evitar que una temperatura excesiva provoque granos gruesos y reduzca el rendimiento de las tuberías, así como para evitar el estrés térmico causado por una velocidad de calentamiento excesiva.
2. Calentamiento uniforme: Asegúrese de que la temperatura en el horno sea uniforme y coloque las tuberías de acero en un lugar adecuado para evitar el sobrecalentamiento local o el calentamiento insuficiente. Para tuberías de paredes gruesas o de mayor diámetro, prolongue el tiempo de calentamiento adecuadamente para garantizar una temperatura constante tanto en el interior como en el exterior.
3. Tiempo de aislamiento: Calcule el tiempo de aislamiento en función del espesor de la pared de la tubería de acero, de 0,5 a 1 hora por cada 10 mm de espesor de pared para asegurar una transformación suficiente de la estructura. Mantenga la temperatura del horno estable durante el período de aislamiento para evitar que las fluctuaciones de temperatura afecten el efecto del recocido.
4. Gestión del enfriamiento: Tras el recocido, se suele optar por el enfriamiento del horno. Cuando la temperatura del horno desciende por debajo de 500 °C, se puede enfriar por aire. La velocidad de enfriamiento del acero con alto contenido de carbono debe ser menor (≤20 °C/h) para evitar la precipitación de carburos de la red. Se debe evitar la deformación de las tuberías de acero o la generación de nuevas tensiones internas causadas por un enfriamiento rápido.
5. Protección atmosférica: Para evitar la oxidación y la descarburación de la superficie de la tubería de acero, se puede utilizar una atmósfera protectora (como nitrógeno o argón) o aplicar un recubrimiento antioxidante. Si se utiliza un recocido convencional en horno de aire, la capa de óxido superficial debe limpiarse a tiempo después del recocido.
6. Equipo y funcionamiento: Revise periódicamente el sistema de control de temperatura del horno de recocido, los elementos calefactores y otros equipos para garantizar su correcto funcionamiento. Los operadores deben cumplir estrictamente las normas de seguridad y usar equipo de protección para evitar quemaduras, descargas eléctricas y otros accidentes.
7. Inspección de calidad: Tras el recocido, la tubería de acero se somete a pruebas de dureza, análisis metalográfico de la estructura y otras pruebas para comprobar si el tamaño del grano y la uniformidad estructural cumplen los requisitos. Si se detecta que el rendimiento no cumple con los estándares, se deben analizar las causas y se realiza un nuevo recocido.