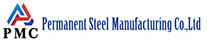
CO2 Corrosion:
CO2 corrosion is a common type of corrosion that plagues the world's petroleum industry as well as the development of my country's oil and gas industry. The most typical feature of CO2 corrosion is pitting, moss-like corrosion and mesa-like corrosion in the local pipeline. Among them, mesa-like corrosion is the most serious corrosion process.
Fe(HCO3)2=FeCO3+H20+CO2
There are many factors affecting CO2 corrosion, such as temperature, CO2 partial pressure, flow rate, alloying elements, CI-, HCO3-, Ca2+ and Mg2+,bacteria, Fe3C concentration, FeCO3 solubility, protective film, heat treatment of pipes, and microstructure have certain effects on corrosion, and the corrosion situation under the influence of multiple factors is relatively complicated.
H2S Corrosion:
Some oil and gas fields contain a large amount of H2S gas, which has a relatively large solubility in water and is highly corrosive. When FeS is dense and closely combined with the metal matrix, it has a certain slow-down effect on corrosion. But when the generated FeS is not dense , It can form a strong galvanic couple with a potential difference of 0.2~0.4V with the metal base, which will promote the corrosion of the base metal. In addition, when there are sulfides in the solution or on the surface of the metal substrate, the sulfides prevent the conversion of hydrogen atoms to hydrogen molecules to a certain extent. These hydrogen atoms combine to form hydrogen molecules at the defects and other parts of the surface layer of the pipe rod and gather and expand. Hydrogen pressure is generated, and under the superposition and synergistic effect of the service tension of the pipe and rod, SSCC (H2S stress corrosion cracking) is formed. The working conditions of the pipe and rod in the oil well, such as the production fluid flow rate, working temperature, stress state, surface defects, etc. can accelerate the corrosion of steel by H2S and SSCC.
Regarding the corrosion of oil and gas pipelines in the H2S-CO2 coexistence system, there are relatively few studies at home and abroad, especially in the high-temperature and high-pressure H2S-CO2 multiphase flow medium. Therefore, it is more important to study the corrosion under the coexistence of H2S and CO2.
Tips: In the application of submarine oil and gas pipeline engineering, ERW welded pipes has the advantages of both safety (good welding quality) and economy.
ASTM A53 Grade B is more popular than other grades. These pipes can be bare pipes without any coating, or it may be Hot-Dipped or Zinc-Coated and manufactured by Welding or by a Seamless manufacturing process. In Oil and Gas, A53 grade pipes are used in the structural and non-critical applications.