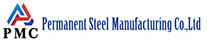
It is important to choose anti-corrosion materials that are suitable for the specific pipe and environment. Common anti-corrosion coatings include epoxy resin, polyurethane, polyethylene and asphalt. When selecting anti-corrosion materials, factors such as the purpose of the pipeline, medium, temperature and pressure should be considered.
For complex or large-scale projects, it is recommended to seek the help of professional anti-corrosion engineers or contractors to ensure the successful completion of the project and compliance with requirements.
Advantages of pipe inner coating:
From the current point of view, the use of internal coating technology for pipelines has the following advantages:
(1) Reduce the internal friction of the pipeline, improve its own performance, improve the fluidity of the pipeline, and improve its working efficiency. At present, most foreign relevant personnel believe that the surface roughness of some typical coated steel pipes is 6.4μm, while the inner surface roughness of new steel pipes is generally 19.1um, and the inner surface roughness of bare pipes is 45μm. When rough When the degree is lower than 90%, the pipeline friction coefficient will be reduced by up to 33%. At this time, the number of pipes will increase accordingly.
(2) Since the friction coefficient of the inner coating pipeline continues to decrease, the pressure difference between the booster stations can be reduced, the distance between stations can be expanded, and the number of booster stations can be reduced.
(3) Save pipe materials and construction costs. Since the roughness of the inner wall of the pipe will be reduced after coating, the hydraulic friction will also continue to change. In this way, when the gas transmission volume reaches a certain level, other conditions will not change, and the designed pipe diameter can be adjusted, which can save a lot of pipe costs and achieve the corresponding purpose.
(4) Reduce transmission power consumption and save fuel costs. According to the corresponding data survey, it was found that after using the inner coating, the power consumption of gas transmission can be reduced by about 20%.
(5) It has a certain protective effect on the inner wall of the tank. In the daily work process, the appearance of some other impurities often causes corrosion in the pipeline, thus affecting the overall quality of transportation.
(6) Do a good job in pipeline inspection. After the pipeline is coated, its inner wall is relatively smooth, and it is also convenient for the corresponding staff to do inspection work and conduct comprehensive inspections for cracks, corrosion and other problems.
(7) Reduce maintenance costs. According to the corresponding data survey, it was found that the driving force of coated pipes is relatively strong, while the driving pressure of uncoated pipes is relatively small, and coated pipes are not easily contaminated with impurities, and are easier to clean during the cleaning process. Reduce the number of cleanings, thereby reducing maintenance fees. In recent years of development, internal coating technology has been applied to original pipelines, which can reduce the amount of deposition by 25%.