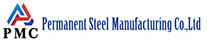
Galvanized square tube is made of hot-rolled or cold-rolled strip steel as blank, which is curled and welded into square steel tube, and then coated with a layer of zinc on the surface through hot-dip or electro-galvanizing process. However, the galvanized steel pipe is made by curling and welding the strip steel into a round pipe and then galvanizing The appearance of the galvanized steel pipe is square, and the zinc layer on the surface has good corrosion resistance, which can effectively resist the erosion of the atmosphere, water and other environments, and prolong the service life of the square tube. It has high strength, stable structure, and certain toughness.
Galvanized square tubes are widely used in the construction industry, such as building structures and scaffolding; in the manufacturing industry, they are used to make furniture and mechanical frames; in the agricultural field, they are used to build greenhouses, etc., and have a wide range of uses.
How to deal with deformation of galvanized square tubes?
During the welding process, metal components such as square tubes often experience welding deformation. This problem is common and needs to be taken seriously. In response to this situation, traditional correction methods mostly rely on fire attack, but when the degree of deformation is large, the effect of this method is often unsatisfactory. Therefore, it is necessary to adopt a more scientific strategy to control and correct welding deformation.
Pre-event support and processing
Before welding, you can build a support structure inside the box with angle steel or square tubes, and then weld it after it is fixed. After welding is completed, if it is found that there are redundant parts or the support is too large, it can be cut off by gas cutting. This can effectively support the structure and reduce the possibility of deformation during welding.
Adjust the welding sequence and method to effectively eliminate stress.
1. Selection of welding power source: Priority should be given to heat sources with concentrated energy. For example, consumable electrode welding is better than manual arc welding. Hot wire TIG welding performs better than traditional consumable electrode welding. In addition, welding methods such as laser welding, plasma welding and electron beam welding also use high-energy concentrated heat sources, which can effectively reduce welding deformation.
2. Adjustment of welding sequence: By adopting appropriate welding sequence such as symmetrical welding, welding deformation can be effectively reduced. During the welding process, the symmetry of the weld should be maintained as much as possible to balance the thermal stress generated during welding, thereby reducing the possibility of deformation.
Anti-deformation technology and strong constraints
1. Welding anti-deformation: Before welding, predict the possible deformation after welding, and reserve a certain deformation margin in the opposite direction to offset the deformation after welding. This is a very effective means of controlling welding deformation.
2. Forced constraint: During the welding process, the deformation of the weld is controlled by applying external force. This work requires professionals and equipment to carry out.
Welding hammering and post-weld treatment
1. Hammering during welding: Hammering is performed immediately during the welding process or after welding is completed. This can effectively eliminate the stress in the welding area and reduce the occurrence of deformation.
2. Post-weld stress annealing: Although the deformation caused by welding cannot be completely eliminated, some of the deformation can be reduced or eliminated through stress annealing. This requires the use of professional heat treatment equipment and corresponding processes.