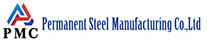
Connecting two seamless steel pipes can be done using several methods, depending on the application, pressure requirements, and specific conditions.
There are two main ways: one is detachable connection and the other is non-detachable connection. Detachable connection refers to disassembly after installation. A non-detachable connection permanently connects two seamless steel pipes together.
Here are some common methods
1. Welding
Butt Welding: This is the most common method where the ends of the pipes are beveled and then welded together using a welding process like TIG (Tungsten Inert Gas) or MIG (Metal Inert Gas) welding.
Socket Welding: One end of the pipe is inserted into a recessed area of a fitting and then welded in place. This is often used for smaller diameter pipes.
2. Threaded Connections
Pipes can be threaded at the ends, and then connected using threaded fittings. This method is typically used for smaller pipes and in applications where disassembly is needed.
3. Flanged Connections
Flanges are welded or threaded to the ends of the pipes. The pipes are then connected by bolting the flanges together with a gasket in between to ensure a tight seal. This method is useful for larger pipes and for systems that may need to be disassembled frequently.
4. Mechanical Couplings
Grooved Couplings: These couplings have grooves at the pipe ends, and a gasket and housing are used to connect the pipes. This method allows for flexibility and quick assembly/disassembly.
Compression Couplings: These use a sleeve and a compression ring to seal and hold the pipes together. They are often used for temporary connections or in situations where welding is not feasible.
5. Push-Fit Connections
This method uses a fitting that allows pipes to be pushed into place without the need for welding or threading. It's common in some plumbing applications but less so in industrial settings.
Steps for Welding Seamless Steel Pipes:
1. Preparation:
Clean the ends of the pipes to remove any dirt, oil, or rust.
Bevel the edges of the pipes if butt welding.
2.Alignment:
Align the pipes accurately to ensure a proper weld. Use clamps or fixtures to hold the pipes in place.
3. Welding:
Select the appropriate welding technique (e.g., TIG or MIG) and filler material.
Weld the pipes together, ensuring good penetration and avoiding defects like porosity or cracks.
4. Inspection:
Inspect the weld for any defects using non-destructive testing methods like X-ray, ultrasonic testing, or dye penetrant inspection.
5. Finishing:
Clean the weld area and apply any necessary coatings to protect against corrosion.
Each method has its own set of tools and equipment requirements, so it's important to choose the right method based on the specific needs of your project.
Read more: Basic Information on Wall Thickness and Outer Diameter of Seamless Steel Pipes