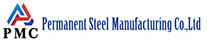
Shearing processing refers to cutting the welded pipe into the required size according to a certain length. Shearing equipment generally includes shears and cutting machines. Shears are suitable for cutting small and medium-sized pipes, while cutting machines are suitable for cutting large pipes. The advantages of shearing are fast processing speed, low cost, and the ability to accurately cut to the required length.
2. Welded pipe chamfering processing
The chamfering process is to better connect the welded pipes. The chamfering process can chamfer both ends of the pipe to make the connection between the pipe mouth and the pipe stronger and prevent water leakage. Common chamfering equipment includes hand chamfering machines and pipe chamfering machines. Chamfering machines usually support processing at various angles and can meet different processing needs, while hand-operated chamfering machines are suitable for processing smaller pipes.
3. Welded pipe cutting processing
The cutting process is to cut the welded pipe into the required shape and size. Cutting equipment usually includes flame cutting machines, plasma cutting machines and laser cutting machines. Among them, laser cutting machines have the highest precision and are suitable for high-demand processing techniques and materials.
The main purpose of grinding welded pipes is to achieve better surface quality. Common grinding equipment include manual grinders and automatic grinders. Manual grinders are suitable for processing small pipes, and automatic grinders are suitable for processing medium and large pipes.
Welded steel pipe processing equipment selection:
Welded pipe processing equipment includes cutting machines, pipe bending machines, stamping machines, sheet metal machines, welding machines, etc. When selecting equipment, you need to consider multiple factors such as product type, processing efficiency, cost, etc., and make a selection based on actual needs.
Welded steel pipe processing technology:
The welded steel pipe processing technology includes four links: cutting, forming, welding and trimming.
1. cutting
The original steel pipe is cut into different lengths according to the design requirements for subsequent processing.
2. Forming
The cut steel pipes are processed by machining, bending and forming to form pipe fittings of various shapes, such as elbows, tees, reducers, etc.
3. Welding
The formed pipe fittings are pre-assembled and then welded and reinforced. The most commonly used welding methods are gas shielded welding and manual arc welding.
4. Trim
After welding is completed, trimming work is required, including burr removal, grinding and polishing, deviation correction, etc., to ensure the accuracy and quality of the welded pipe.
Conclusion:
The processing of welded steel pipes involves a variety of processing methods, and different processing equipment and process operations are selected according to different needs. The processing quality of welded pipes is related to the later use effect, and attention must be paid to accuracy and surface quality.