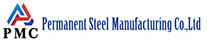
In many scenarios of industrial manufacturing and daily life, 316 stainless steel pipes are widely used in chemical industry, marine engineering, medical equipment and other fields due to their excellent corrosion resistance, good high temperature strength and excellent processing performance. However, some problems may occur during the processing of 316 stainless steel pipes. For example, after processes such as cold processing, welding, and straightening, processing stress will be generated inside the material, which will affect the mechanical properties and dimensional stability of the material. In severe cases, it may also cause product deformation and cracking. Moreover, after processing or use in a high-temperature environment, an oxide layer is easily formed on its surface, which not only affects the appearance but also reduces corrosion resistance. To solve these problems, bright annealing process is needed.
What is 316 stainless steel pipe bright annealing?
Bright annealing of 316 stainless steel pipe is a heat treatment process carried out in a protective gas environment to eliminate processing stress, improve material structure and obtain a bright surface without oxidation. This process ensures that the 316 stainless steel pipe has excellent corrosion resistance, mechanical properties and smoothness after annealing by precisely controlling the temperature, atmosphere and cooling rate. It is widely used in chemical industry, marine engineering, food machinery and other fields.
Analysis of core process parameters
1. Temperature control: The solution treatment temperature of 316 stainless steel is usually set at 1050-1150℃, which allows the carbides to fully dissolve in austenite. It should be noted that too high a temperature can easily lead to coarse grains and affect surface finish; If the temperature is too low, carbides will not be fully dissolved, thus reducing corrosion resistance. In actual operation, the insulation time needs to be adjusted according to the thickness of the pipe (such as 1 hour of insulation for every 25mm thickness).
2. Cooling rate: Rapid cooling is the key to avoid carbide re-precipitation. The cooling rate is required to be ≥55℃/second, and the pipe is quickly passed through the 550-850℃ sensitive temperature zone through a strong convection cooling system (such as segmented air cooling or water cooling) to ensure that the final structure is uniform austenite.
3. Shielding gas selection: High-purity hydrogen (H₂) is used as the protective gas and mixed with nitrogen (N₂). The dew point of hydrogen needs to be strictly controlled below -60°C to prevent oxidation of alloy elements such as chromium and titanium. The pressure inside the furnace is maintained at a positive pressure of more than 20kPa to prevent the infiltration of external oxygen.
4. Furnace sealing and structure: Annealing furnaces need to be equipped with precision sealing systems (such as muffle tube design) to ensure that the gas leakage rate is less than one part per million (ppm level). The heating zone uses Swedish Kanthal heating wire with a temperature control accuracy of ±1°C, and the spiral airflow design ensures that the pipe is heated evenly.
Equipment and Operation Notes
1. Device Configuration:
It adopts horizontal or vertical bright annealing furnace, equipped with PLC control system and 10-inch touch screen, supporting segmented temperature control and real-time monitoring. The cooling section is divided into three zones to independently adjust the air volume and realize plate shape control along the width of the pipe. Equipped with hydrogen ignition device, vacuum system (vacuum degree - 0.1MPa) and double pressure relief protection (electronic + mechanical).
2. Pre-processing and post-processing:
Before annealing, it is necessary to thoroughly degrease and clean (such as ultrasonic treatment with SC2286 cleaning agent) to remove contaminants such as rolling oil. After annealing, the surface finish can reach Ra≤0.4μm, which can meet the BA grade standard without additional polishing.
3. Common Problems and Solutions:
Oxidation problem: Check the sealing of the furnace body to ensure the purity of hydrogen and the maintenance of positive pressure.
Coarse grains: shorten the holding time or optimize the cooling rate.
Uneven plate shape: adjust the air volume distribution in the cooling section and stabilize the line speed through the tension roller control system.
Application advantages and industry value
1. Improved surface finish: Directly replaces the polishing process and reduces costs.
2. Enhanced corrosion resistance: Reduces the surface chromium-depleted layer, suitable for harsh environments.
3. Optimization of mechanical properties: eliminating stress, improving ductility and fatigue resistance.
Application areas
1. In the chemical industry, it is used for the manufacture of pipelines and reactors for conveying various corrosive chemical media. Due to its excellent corrosion resistance, it can effectively resist the erosion of chemical substances and ensure the safety and stability of chemical production.
2. In the food industry, the bright surfaces of pipes and containers used in food processing equipment not only meet food hygiene requirements and are easy to clean, but also prevent the adhesion of impurities and ensure food safety.
3. In the medical field, it is often used to manufacture medical devices, surgical instruments, etc. Its good biocompatibility and corrosion resistance will not have adverse effects on human tissues. At the same time, the bright surface is also easy to disinfect and maintain.
Read more: 316L Stainless Steel VS 304 Stainless Steel: in Corrosion Resistance