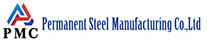
316 stainless steel is a grade of stainless steel produced according to American ASTM standards. 316 stainless steel is widely used in chemical, shipbuilding, medical and other fields due to its excellent corrosion resistance and high strength. However, in the actual welding process, 316 stainless steel often cracks. This not only affects the quality of the project, but may also lead to serious safety hazards. Here we will analyze the causes of 316 stainless steel welding cracking.
316 stainless steel material issues
1. The quality of the material itself
The quality of the material is an important part of the welding process. If there are impurities, pores or microcracks inside the 316 stainless steel, these defects are easy to expand during the welding process and eventually lead to cracking.Therefore, it is very important to choose high-quality 316 stainless steel materials, and the supplier's reputation and material inspection report should be an important basis for purchasing decisions.
2. Uneven material thickness
Uneven thickness of welding materials will lead to thermal stress concentration, especially in areas with large thickness differences, which are more likely to form cracks. Therefore, during design and construction, welding structures with large thickness differences should be avoided as much as possible.
316 stainless steel welding process
1. Insufficient preheating
Insufficient preheating of 316 stainless steel before welding will lead to excessive temperature gradient in the weld area, resulting in thermal stress and cracks. Preheating can reduce temperature gradients and reduce thermal stress. It is recommended to preheat the thick plate appropriately before welding, and the preheating temperature is generally controlled at 100-150℃.
2. Improper welding parameter settings
Improper settings of welding current, voltage, welding speed and other parameters are important causes of cracking. For example, excessive current or too fast welding speed will cause the weld metal to cool too quickly and form thermal cracks. Therefore, appropriate welding parameters should be selected according to the thickness and structure of the material to ensure the quality of the weld.
316 stainless steel welding material selection
1. Mismatched welding materials
Using welding materials that do not match 316 stainless steel will lead to inconsistent mechanical properties of the welded joint and increase the risk of cracking. Welding materials that match the performance of 316 stainless steel should be selected, such as welding materials containing Mo elements, to improve the crack resistance of the weld.
2. Welding material quality issues
The quality of the welding material itself also affects the welding quality. Poor quality welding materials may contain impurities or pores, causing welding cracks. Therefore, choosing high-quality welding materials and ensuring the purity and consistency of the welding materials are important measures to prevent cracking.
316 stainless steel welding environment
1. High humidity in the welding environment
A high humidity environment will cause oxidation in the welding area, increasing the possibility of cracking. Therefore, when welding 316 stainless steel, the welding environment should be kept dry and clean, and welding should be performed indoors or in a closed environment as much as possible.
2. Insufficient gas protection
Insufficient gas protection during welding can easily lead to oxidation of weld metal and cause cracks. It is recommended to use a high purity shielding gas such as argon and ensure that the gas flow and coverage area are adequate to avoid oxidation issues.
316 stainless steel welding post-processing issues
1. Too fast cooling rate
Too fast cooling rate after welding will cause stress cracks in the weld area. Especially for thick plate welding, the cooling process should be carried out gradually to avoid sudden cooling and heating. Slow cooling method can be adopted, or insulation treatment can be carried out immediately after welding.
2. Improper heat treatment
Heat treatment after welding is an important means to release welding stress. For 316 stainless steel, the appropriate heat treatment process should be selected according to the actual situation, such as annealing, to eliminate welding residual stress and prevent the occurrence of cracks.
The problem of 316 stainless steel welding cracking is a complex engineering and technical problem, involving materials, processes, welding materials, environment and post-processing. By selecting high-quality materials, optimizing welding processes, choosing suitable welding materials, improving welding environment and performing appropriate post-processing, welding cracking can be effectively prevented, welding quality can be improved, and the safety and reliability of the project can be ensured.
Read more: Causes and Detection Methods of 316 Stainless Steel Pipes Leakage