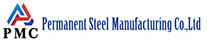
In various piping systems, stainless elbows are like a key hub. Although they seem ordinary, they play an irreplaceable role. It is a bent pipe fitting used for pipe connection. Through cold bending or hot bending process, the stainless steel material is formed into the required shape to achieve the change of pipe direction.
Common stainless steel elbow materials include 304, 316, etc. 304 stainless steel has good corrosion resistance and versatility and can remain stable in general environments; 316 stainless steel, due to the addition of molybdenum, performs better in resistance to pitting corrosion and chloride ion corrosion, and is often used in more severe corrosive environments. In industrial piping systems, stainless steel elbows are widely used due to their good corrosion resistance and high strength. However, in some special working environments, such as earthquake-prone areas or places with frequent mechanical vibrations, stainless steel elbows also need to have good impact and seismic resistance to ensure the stability and safety of the entire system.
In order to improve the impact and seismic resistance of stainless steel elbows, designers usually take the following methods:
1. Material selection: Choose stainless steel materials with high toughness and high elasticity, such as 304L or 316L stainless steel. These materials not only have excellent corrosion resistance, but can also absorb more when impacted by external forces, reducing the risk of cracks and breakage.
2. Structural optimization: By optimizing the geometric shape and wall thickness distribution of the elbow, its overall rigidity and anti-deformation ability are improved. For example, using a thickened wall design or adding reinforcing ribs can effectively disperse stress and reduce local concentrated stress.
3. Welding process: Use high-quality welding technology to ensure the strength and uniformity of the weld. Advanced welding methods, such as TIG (Tungsten Inert Gas) and MIG (Metal Inert Gas), provide more reliable connections and avoid weld cracking under shock and vibration.
4. Surface treatment: Appropriate surface treatment of stainless steel elbows, such as sandblasting or polishing, can remove surface defects and improve its fatigue resistance. In addition, coating treatment can further improve its corrosion resistance and wear resistance.
5. Simulation test: Through computer simulation and actual testing, the performance of stainless steel elbows under different shock and vibration conditions is verified. This helps to identify potential design flaws and make improvements accordingly.
Through the above design and manufacturing measures, the stainless steel elbow can remain stable in various harsh environments and effectively resist the impact of shock and vibration. This not only improves the overall reliability of the system, but also extends the service life of the equipment and reduces maintenance costs.
Read more: Stainless Steel Elbows: Good Performance in Resisting Harsh Environments